The cellulose ether is the powdered cellulose ether generated by reactions with such etherification agents as ethylene chloride, propylene chloride, and ethylene oxide after chemical treatment, with wood fibers and refined short cotton fibers as the main raw materials.
The ionic cellulose (carboxymethyl cellulose salt) is unstable in the presence of calcium ions, so the ready-mixed mortar with cement and slaked lime as the cementitious materials is rarely used. Hydroxy ethyl cellulose is also used in certain ready-mixed mortar, but its market share is very small.
The water retention and thickening effects are in that order: hydroxy propyl methyl cellulose ether(HPMC)> hydroxy ethyl cellulose ether (HEC)> carboxymethyl cellulose (CMC). Table 2-11 shows the technical requirements of cellulose ether in the construction ready-mixed mortar.

The cellulose ether is a major additive in ready-mixed mortar. Though the addition amount is very low, it can significantly improve the performance of mortar. It can improve the consistency, performance, adhesion properties and water retention properties of mortar, and plays a very important role in the field of ready-mixed mortar. Its main characteristics are as follows.
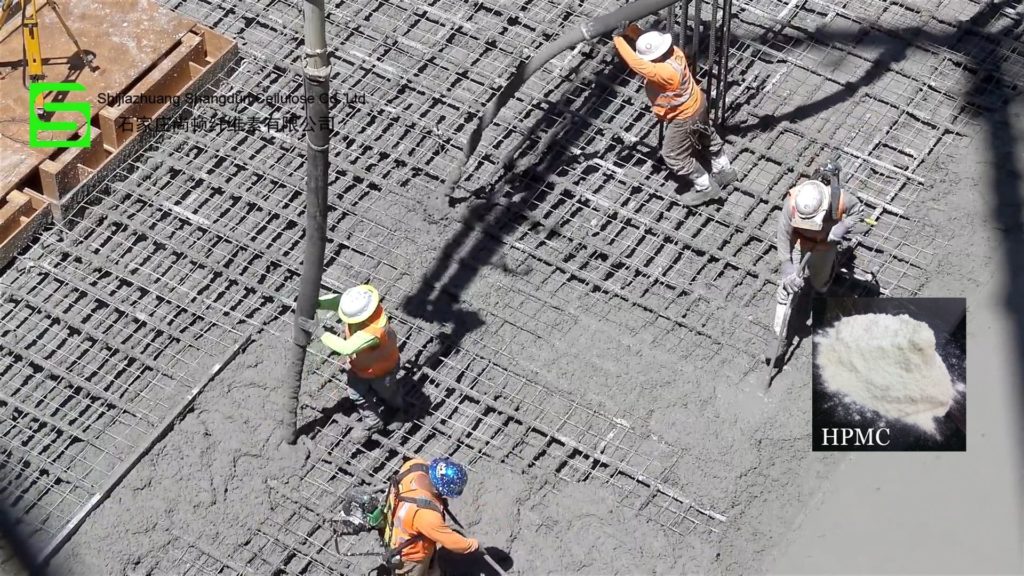
- Excellent Water Retention
Water retention is one of the important indicators of quality of cellulose ether, and especially in thin-layer construction it is more important. Improving the water retention of mortar mortar can effectively prevent drying due to excessive water loss, and prevent the decrease in strength cracking phenomena resulting from inadequate hydration of cement. Factors affecting the water retention of mortar include the dosage of cellulose ether, viscosity,
fineness and operating environment. Generally the higher the viscosity is, the finer the fineness is and the larger the dosage is, then the better the water retention will be. The water retention of cellulose ether is related to the etherification degree of cellulose. The higher the content of methoxy group is, the better the water retention will be.
- Strong Adhesion and Good Sag Resistance
The cellulose ether has a very good thickening effect. The addition of cellulose ether in the ready-mixed mortar can increase the viscosity by several thousand times, make the mortar have better adhesion, and can make the pasted tiles have better sag resistance. The viscosity of cellulose ether can affect the bonding strength, mobility, structural stability and workability of mortar.
In general, the higher the viscosity is, the better the water retention effects will be. However, When the viscosity and the molecular weight of cellulose ether are higher, its dissolution performance will be reduced accordingly, which has a negative impact on the strength and construction performance of mortar. The higher the viscosity is, the more sticky the wet mortar will be. It will be easy to stick the scraper, of little help for increasing the structural strength of the wet mortar itself, and not obvious in improving sag resistance performance.
- Solubility
Since the surface particles of cellulose ether are specially treated, its solubility is very good both in the cement mortar and plaster, or in the paint system. It is difficult to agglomerate and the dissolution speed is fast.
In the ready-mixed mortar, the cellulose ether plays a role in water retention, thickening, improving the construction performance and other aspects. The good water retention can avoid the sugaring as well as dusting phenomena and decrease in strength resulting from lack of water and incomplete hydration of cement. The thickening effects can make the structural strength of new mixed mortar greatly enhanced and make the pasted tiles have good sag resistance. The addition of of cellulose ether can significantly improve the viscosity of wet mortar, and have have good viscosity to various substrates, thus improving the performance of the wet mortar on the wall and reducing waste.